6 Steps to Mastering the Organization of Your Equipment
Equipment organization will make you better, faster, and more creative.
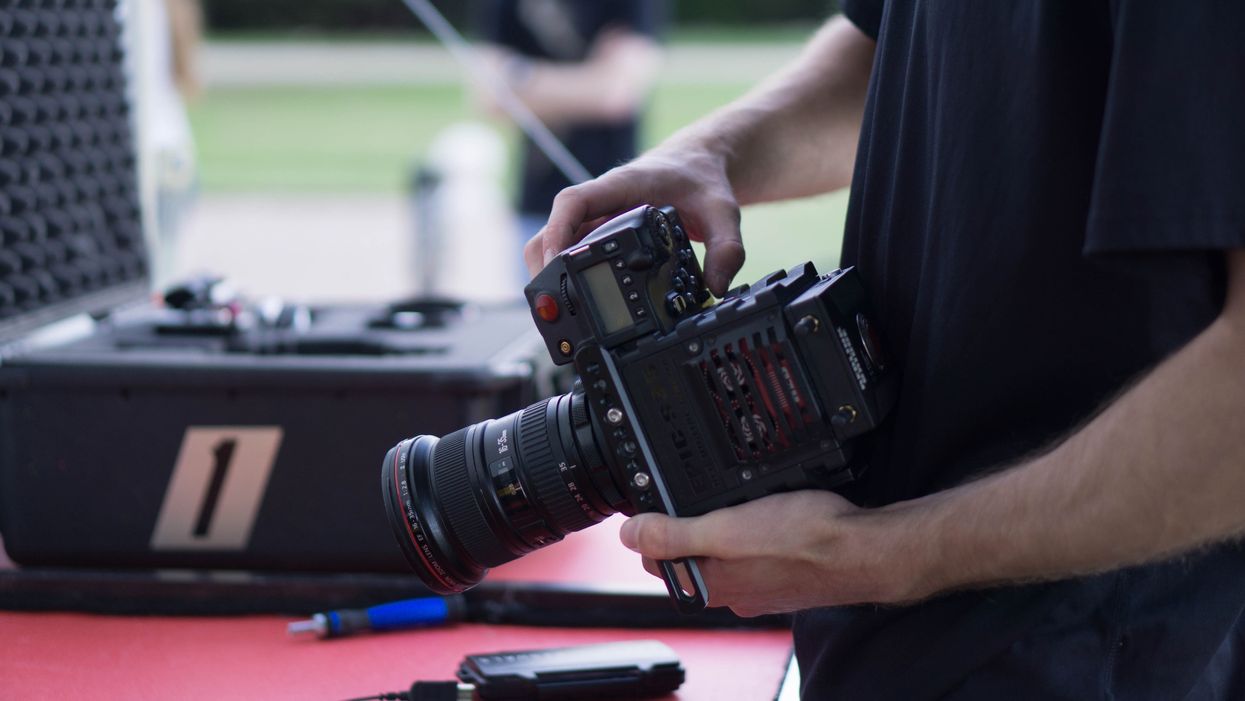
As your sets get bigger, your shots become more complicated and you acquire more equipment, paying attention to details like keeping everything organized, clean, and in dedicated places can result in huge time savings and, most importantly, keep all of that beautiful and expensive camera gear safe. In this post, I'll walk you through the equipment management system that my team at Fractal Visuals has developed for our video production company.
At Fractal Visuals, we are proud to own and operate some of the best equipment in the industry including RED Cinema Cameras, Wunder Audio microphones, and Freefly Systems Gimbals and Drones. One of the biggest challenges we face using this equipment is in management and logistics. Over the last few years, we've been working to develop the perfect system for equipment management.
The resulting system delivers the perfect balance of efficiency while also keeping things safe, organized, and taking up the smallest amount of space possible.
Here are the key factors we identified for creating the best organization system:
- Optimal cases for each kind of equipment
- Naming/numbering system
- Organization of the containers
- Case selection
- Spare parts and backup equipment management
- Strategic organization
John Byron Hanby IV using the accessory case to adjust RED Dragon camera.Credit: Anna Owens
Guiding principles
When I was young, may Dad drilled a motto into my brain: attention to detail, sense of urgency, keep it simple. Today, it is one of the driving forces behind everything I do. Taken in the context of equipment management it breaks down as follows:
Attention to detail:
Paying attention to details like keeping everything organized, clean, in dedicated places, and always putting it back in the exact same place can result in huge time savings and most importantly keep all of that beautiful and expensive camera gear safe.
Sense of urgency:
Our sets move incredibly quickly. We don’t waste time, and having a sense of urgency in accomplishing our goals is a huge driving force behind this speed. Localizing all key components on an equipment-specific basis (such as keeping all drone spare parts and accessories in one case) is a lifesaver when you're moving fast or there is pressure to deliver something perfectly the first time.
Keep it simple:
When working on a production, the last thing you want it to have a complicated system for finding the equipment you need. Keeping it simple ensures you’ll be able to quickly communicate what you need, and where it is, and know it will always be in that place.
Fractal Visuals Team Begins to Setup for ShootCredit: Anna Owens
1. Optimal cases for each kind of equipment
We use two different kinds of cases in our equipment organization:
- Pelican Cases for the main pieces of equipment
- Hardware organization cases for all of the miscellaneous parts, accessories, adapters, screws, and so on
Where possible, I’ve included Amazon links to everything we use further down in this article.
2. Naming/numbering system
True to the "keep it simple" philosophy, our numbering system was created based on being simple and easy to communicate to anyone regardless of their experience on set. When my DP Michael Castoro needs something, he can simply say “Bring me case #1.” There is no need to describe the size of the case, what it looks like, or what is in it because it’s clearly labeled.
As your equipment expands, you need to maintain strategy in numbering your cases, ensuring there is a logical progression to how things are labeled, and in a way that makes sense ("attention to detail") so that you and your crew can easily remember what goes where.
Our numbering system is based on order of importance, with number one being the most important case and number nine holding the lesser used equipment. We always put our RED cameras in case number one.
Our Freefly Movi goes in case number two because our main focus as a video production company is music videos and the majority of our shots are highly dynamic and utilize gimbal stabilization.
Our Freefly Alta drone goes in case number three.
Each of these bigger cases has a corresponding smaller case. Those cases are labeled 1a, 2a, 3a, and so on.
Fractal Visuals Case Numbering SystemCredit: John Byron Hanby IV
Here is a complete breakdown of our case numbering system to give you a better idea of how it’s structured:
1. Camera & lenses
1A. Filters, LCD cables, tripod plates, mounting screws, regular and philips screwdrivers
2. Movi Gimbal
2A. Gimbal spare parts, flexible HDMI, flexible LCD cables, Movi screwdrivers
3. Alta Drone
3A. Drone spare parts, drone screwdrivers
4. Drone Battery Charger
4A. Charger spare parts, Li-Po paraboards, Misc. charging cables
4B. AC Charging cables, DC power bricks
5. Walkie talkies, gimbal and drone remote controls and other transmission equipment
6. V-Mount batteries & battery accessories
7. “Oh S#*! I broke something" case (Power tools, zip ties, super glue, duct tape and other repair equipment)
8. Drone batteries *This one is kept separate because it's the heaviest and most dangerous case because of the lithium polymer batteries - which can explode if mishandled.
9. Light stands, extension cords and backup tripods
10. Hardware (Screws, bolts, washers, nuts, and anything else needed to mount the camera where ever you need)
When something breaks or you need to switch mounts, you can easily communicate the case needed to one of your crew members by saying “Bring me case 1a,” or “Bring me the PL mount in case 1a.” This eliminates confusion. Also, always remember your manners; just because you're on a fast moving film set doesn't mean you don’t have time to say “Please” or “Thank you.” Small things like that will make your crew feel more valued, and in turn cause them to work harder to help make your vision a reality.
There is no need to describe the size of the case, what it looks like, or what is in it because it’s clearly labeled.
How to set up your own case numbering system:
- Identify the key pieces of equipment for your specific shooting style and needs.
- Label and organize the equipment in that order.
- Put supplementary accessories in separate cases with the corresponding number.
- Always put each piece of equipment back in the exact place you found it
- Designate places both in your studio and when on the road that will always be the home for each case.
3. Organization of the containers
After you have organized your equipment and put it into containers, you need to develop a system for organizing the containers and designate places where they “belong.” This will speed up your checklist to ensure nothing is left behind. For example, I always put Case One right behind the passenger seat in my truck. Case Nine goes behind the driver seat and so on.
When on large shoots that require our Mobile Command Center (a separate article coming on that in the future...), we pack our cases in order of importance, placing the largest, highest number cases like Eight and Nine in the back, and everything else stacked in order, with the camera being closest to the front of the trailer. This way, when we arrive on set, the first thing that comes out and the last thing that goes in is always the camera.
This ensures the equipment is always accounted for, and the most expensive gear is not lost or otherwise mistreated throughout the production process.
John Byron Hanby, IV Carries Camera Case Number 1Credit: Anna Owens
4. Case selection
Cases are expensive, but they're worth their weight in gold because of the safety and peace of mind they provide. Whether it's protecting your valuable equipment, keeping everything organized, or making it easy to load and unload all of your gear in a time-efficient manner, the investment is well worth it.
Links to some of our top cases:
- Large Dewalt case (Accessories)
- Medium Dewalt case (Accessories)
- Small Dewalt case (Super tiny spare parts)
- Dewalt tool case (Hammers, power tools, etc.)
- Pelican 1510 (V Mount batteries)
- Pelican 1550 (Camera Body)
- Pelican 1640 (Drone Batteries)
Of course, you may find other that you like better, but after years of experimentation, these work best for us.
5. Spare parts and backup equipment management
Having spare parts and a backup of everything may not always be an option. But as your budget continues to increase, and your ability to house larger amounts of equipment and those backup resources also increases, there's value in knowing that—even if something goes terribly wrong and your $60,000 drone rig crashes in the middle of the desert—you'll still be able to finish filming and deliver your project to the client. While not everybody will be working with $60,000 drone rigs, the same thing can be said for all of the small spare miscellaneous parts that come along with it, as those are just as prone to breaking, and in some cases, one $15 part can stop the entire $60,000 rig from working at all.
Meticulous organization takes time and lots of planning, but it only needs to be done once.
The most obvious example of this part would be an ultra thin flexible HDMI or SDI cable that routes out from your camera to your video monitoring system that transmits from the drone. Another could be a spare screw for pieces of equipment that may be under high stress loads and prone to vibrations, causing screws to fall out. Fortunately, our team hasn't yet run into these kinds of problems, but we are always prepared.
A Look Inside Case 1ACredit: John Byron Hanby, IV
These replacement parts may not seem very important at first, until you're out in the middle of nowhere with no access to any kind of repair materials and one of those small pieces fails. Therefore, it's always a good idea to prepare for the worst and hope for the best. Spare parts can be tiny and pieces like gimbal screws can easily be lost. The case that I use for my gimbal accessories and equipment is 2a, and within 2a I have a smaller case that is specific for all of the miscellaneous screws and other “too tiny for a normal size container” parts to be put in.
6. Strategic organization
Meticulous organization takes time and lots of planning, but it only needs to be done once.
With every new addition of equipment, the system can easily be expanded by sticking another number on another Pelican Case and another number on your support case, and you're good to go.
The easiest form of number identification is to use large, easy to read mailbox numbers. These are both inexpensive and also large enough to easily read and apply quickly to each case. We also went overboard on the amount of numbers placed on each case, putting each number on every side of the case. This guarantees that no matter how the case is stacked, covered, or put away, somebody will be able to identify it quickly and get it to the person requesting it as soon as possible.
One other benefit to the numbering system over a traditional alphabet name system comes into play when you're working on location in a crowded or public area. On bigger sets, not having expensive equipment cases labeled with what is inside reduces the likelihood of something being stolen, because only your crew will know what's in each case.
Overall, this organization system has increased our efficiency significantly and reduced the stress levels associated with production. I am beyond thrilled with the results.
What gear organization tips do you have to share? What works best for you? Let us know in the comments.