You Can Make This Amazing Portable Battery Bay at Home
There's a stylish and easy way to charge all your batteries at once.
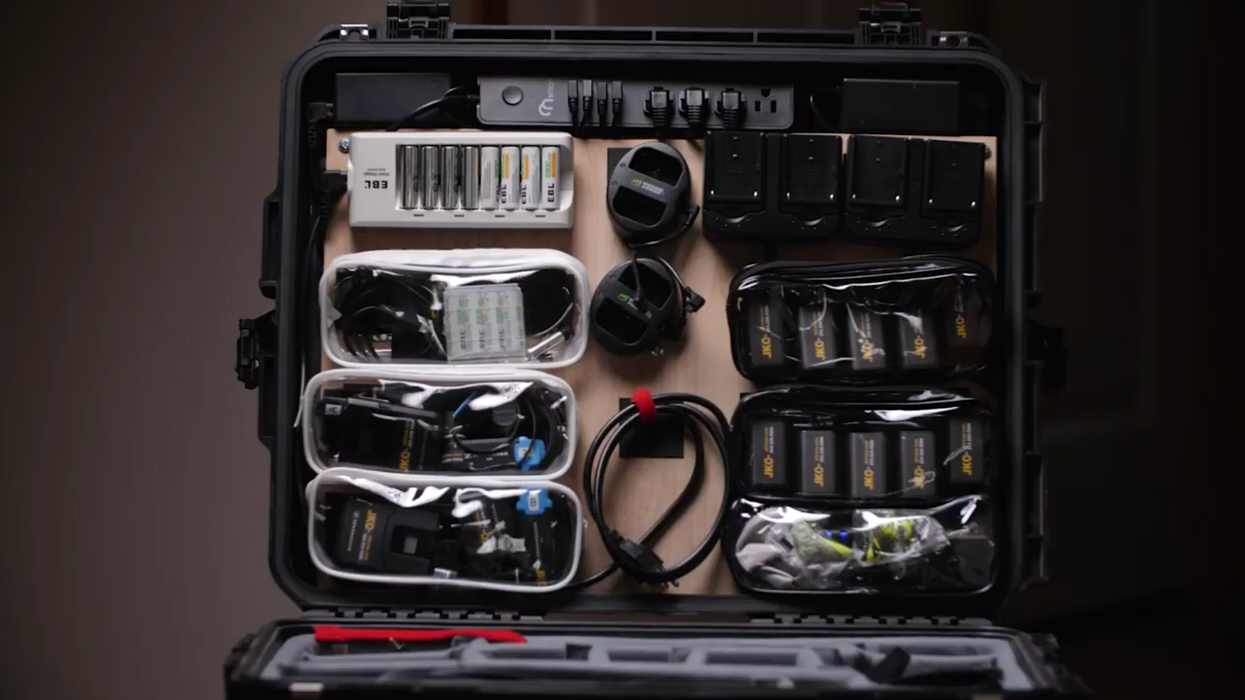
Remember that time we were all stuck inside for a year (give or take)?
Well, I got really bored and decided to build a portable battery bay that would fit inside of my camera case! Charging batteries on the road is beyond annoying. There are way too many cables and varying battery types to keep things clearly organized. So I set out to create a device that would allow me to plug in one cord and charge all of my unique batteries.
Check out the process in my video below.
Specific Components
I kept the video fairly surface level because I didn’t want to bore people with specifics, and everyone is going to require different components that will work best for them. We all have different cases and different batteries, so it simply didn’t make sense for me to show every single step of the process.
That said, I’ve had numerous people reach out requesting a list of the components so that they can create their own portable battery bays, so here are the deets!
Credit: Jacob Christensen
- Power Strip ($30): I searched far and wide for the perfect power strip. I required a lot of USB charging ports, because I charge my camera batteries, wireless microphones, and generic battery bricks all using a Micro USB connection.
- Right Angle Micro USB Cable ($7): It actually took me a long time to find a Micro USB cable that was both a right angle (I wanted a lower profile so that the case could easily close) and long enough to reach all of the charging points in my design.
- Sony L Series Battery Charger ($30): These chargers came with a set of batteries I purchased years ago, and they’ve worked great. There are tons of options out there, though, so find whatever works best for you (you may already own it) and use it!
- 12V Power Supply ($14): I like the charging stations that came with my Sony L Series (NP-F750) batteries, but the wall plug that came with them was too big and clunky, so I found these power supplies to replace them. The original power sources were too wide on the power strip and also too tall, preventing the case from easily closing.
- Right Angle Power Cord ($6): You may have realized that the 12V Power Supply listed above still utilizes a power cord that is perpendicular to the power strip, thus making it difficult to close the case and not crush the cord in the process. These right-angle power cords were my solution; they allowed for a low profile when closing the case and came in varying lengths which made customizing the case easy. I used three of these in my build. Two went to the Sony L Series battery chargers, and one went to my AA/AAA charging station.
- AA Battery Charger w/ Batteries ($22): These rechargeable batteries have been very helpful to include as part of my kit because you never know when you’ll need a set of AAs or AAAs!
- Transparent Pencil Cases ($12): I’ve thoroughly enjoyed how these have played out. Not only can I easily see through the cases, but the velcro design makes the storage very modular. It’s common for me to remove one of the transparent pencil cases, which contains a full lavalier audio kit, and hand it to my audio engineer so that they easily have everything they need. It’s an efficient and cheap solution for storing gear.
- Adhesive Velcro ($17): Make sure you get adhesive velcro. Some velcro comes with nothing on the back so that it can easily be sewn onto cloth, but we like that sticky stuff for ease of use!
- SKB Camera Case ($426): This is by far the most expensive part of the build. The case is sturdy, great for traveling, and I’ve been using mine for four years now. I’ve enjoyed using the case so much that I actually just purchased a second case for our company’s growing gear needs.
All in all, I probably spent around $150 to create the portable battery bay (not counting the case because I already owned it). Yes, the cost associated with this build isn’t necessarily cheap, but goodness gracious, the ease of use has absolutely changed my life. I save so much time and hassle now that I don’t have to worry about packing all of my varying cables—if I bring my camera case, then I know I’m covered!
My biggest piece of advice is to do a lot of brainstorming. I pivoted the design of the build multiple times because I kept coming up with better ideas. It is incredibly helpful to let ideas simmer with a bigger design like this, so go slow and take your time considering what will work best for you.
The build has held up incredibly well so far, and it is always an eye-catcher on set. Clients and crew members always get a kick out of the custom build!
If you have more questions about the build that can’t be answered through the video or the list of components and diagram above, feel free toreach out through our contact page. Always happy to help.